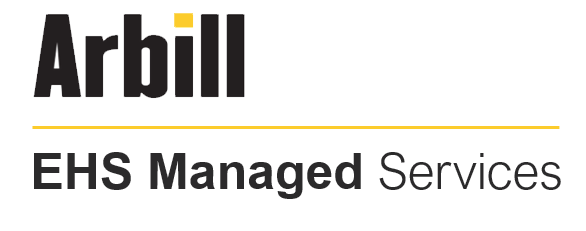
More than 60 OSHA compliance and safety training programs as well as site assessments, audits, staff augmentations, industrial hygiene services and more.
More than 60 OSHA compliance and safety training programs as well as site assessments, audits, staff augmentations, industrial hygiene services and more.
Whatever your industry, Arbill is committed to helping your company ensure workplace safety and lower your regulatory compliance costs with a full suite of consulting options, including site assessments and audits, gap analysis, staff augmentation and industrial hygiene services. All services are provided by highly experienced and certified EHS professionals.
Our team of EH&S professionals conducts a systematic, documented and objective analysis of your site and operations to develop an improvement plan for your business. The team also reviews your written programs, employee training records, inspection forms and injury logs to identify any regulatory or safety gaps that put your workers at risk.
Our team of Certified Hygienists uses environmental monitoring and analytical methods to detect levels of worker exposure, while also providing the information you need about the links between hygiene and common workplace safety hazards. After identifying the sources of your potential problems, our team puts a customized plan in place to protect your employees.
When you've been the subject of a recent OSHA inspection or received a notice of enforcement from state or federal regulators, you need a safety partner to minimize your associated costs. Arbill's consultants advocate on your behalf directly to the agencies involved and work to reduce your fines and workers' compensation premiums. This helps your business improve its focus on safety and reduce its penalties.
Excessively loud workplace environments don't just pose a risk to your workers' eardrums; they threaten their overall safety as noisy environments often lead to other injuries. Arbill's Hearing Conservation consultants identify the noise levels in your facility, design a program to ensure safe exposure for your employees and provide the latest cutting-edge hearing protection technology. This helps you improve workplace safety and comply with OSHA standards.
Heat stress, from exertion or hot environments, places workers at risk for illnesses such as heat stroke, heat exhaustion and cramps. Arbill's Heat Stress consultants help you understand the risks your employees face and develop programs to maximize their heat protection. They also assist you with implementing the program and provide personal protective equipment and heat-stress defense products to ensure your workers are safe from the heat.
Acquiring the right personal protective equipment for your business is critical to the health and safety of your employees. Arbill's Safety Specialists and Safety Account Managers identify exactly the right PPE you need for every aspect of your business. They then provide information and training to your managers and employees to ensure proper use of the equipment, as well as develop job-specific plans for equipment selection and maintenance.
When your entire organization needs a safety upgrade, Arbill's safety consultants are ready to assist you with making safety and compliance core values for your whole business. With our Comprehensive Safety Program Development initiative, our safety consultants assess your company's culture and commitment to safety, create policies and programs to enhance safety, and develop an internal communication plan to reinforce a culture of safety and improve your employee engagement.
Having a robust Environmental Management System (EMS) helps your company confirm compliance with applicable regulatory standards and pinpoint gaps in your compliance programs. While Arbill is not an ISO third-party registrar or certifying consultant, our Environmental Consultants are able to help you build an EMS that complies with ISO 14001 standards of excellence.
Having your business identified as a Potentially Responsible Party (PRP) at a state or federal Superfund site may be a cause of stress or even panic. Arbill's consultants are able to help guide you through this process and assist you with your response to the regulators or PRP group that notified you of your involvement. This helps protect your company and minimize your exposure.
Increasing sustainability in your business isn't just about helping the environment. In today's economy, it's also proving to be a sound business strategy. Starting or strengthening your business' sustainability program helps you reduce waste, attract business from global customers and enhance profitability. Arbill's consultants help you set up your sustainability program with an emphasis on boosting your bottom line, increasing customer retention, strengthening employee engagement and establishing you as a sustainability leader in your industry.
(4 hours)This course is designed for non-medical personnel that require training in Basic First-Aid. The course includes American Heart Association guidelines for basic first-aid injuries and the proper use of PPE. Upon completion of this course, students receive a nationally recognized course completion card that is valid for two years.
(3 hours) This course is designed for non-medical personnel that require training in Adult CPR/AED. The course includes proper use of AEDs and PPE. Upon completion of this course, students receive a nationally recognized course completion card that is valid for two years.*Maximum number of 10 employees per class per American Heart Association.
(4 hours) Training on NFPA 70E for standard electrical and Arc Flash hazards specific to operators and maintenance personnel who are required to function and work in and around Arc Flash boundary zones and interface with electrical equipment.
(4 hours) This course is instructor-led classroom training offering employees a comprehensive overview of basic spill response planning and management. Your team will learn about the prevention of spills, how to proactively plan for an event, proper response procedures and regulatory reporting requirements. This awareness-level class is not a substitute for HAZWOPER Spill Responder Training [29 CFR 1910.120(p)(8)(iii)] that is required for spill response teams, but is a great supplement for other employees.
Awareness for all Employees (1 hour), Affected Employee (2 hours), Healthcare Workers (4 hours)These courses, with varying degrees of detail, instruct participants on the basics of bloodborne pathogens and how they affect the workplace. Generally, the awareness-level training covers the epidemiology, symptoms, transmission and prevention of bloodborne pathogens. The more detailed classes get into exposure control programs, engineering controls, decontamination methods, disposal requirements and recordkeeping related to bloodborne pathogens.
(16 hours)This course is a comprehensive overview of fall protection and prevention in construction and general industry. It covers the employer's duties to provide the correct type of fall protection or fall arrest equipment for employees. This is hands-on training in regard to your specific equipment, exposures and operations. This training will be a key part of an employer's determination of whether or not an employee will qualify as an OSHA "Competent Person."
(8 hours) Any employee that is involved with permit-required confined space entry duties requires training prior to initial duties and in the event of operational change. This training is designed to teach workers their responsibilities for safe confined space entry and to recognize potential hazards and health effects. The employees will also learn how to properly select PPE and monitoring equipment. Both classroom activities and confined space entry drills are conducted.
(8 hours)Highly specialized training that provides participants with the fundamentals of rescue operations, confined space hazards assessment risk management and other tactical considerations. This is a highly customized training for your response team and covers ropes, knots, riggings, belaying, hauling and extrication. *Prerequisites include First Aid/CPR/Bloodborne Pathogens and Confined Space Entry.
(4 hours)This training course includes discussion and hands-on activities for the identification of hazardous materials and education of your employees about how to meet the regulatory requirements for packaging, marking and labeling hazardous materials. Additionally, participants gain a working understanding of shipping papers, placards, safety and security requirements.
(1 hour) Instructor-led classroom training that focuses on electrical safety in the workplace. Identifies electrical hazards, risks and work practice control measures for employees.
(4 hours)Training is required for individuals responsible for ensuring compliance with hazardous waste regulations, and includes discussion and hands-on activities related to proper container management, storage procedures, the use of the hazardous waste manifest and necessary emergency response. This course is designed for employees in direct contact with managing hazardous waste, but is recommended for all employees in a business that generates hazardous waste.
(1 hour)This course is designed for any employee whose job involves performing repetitive tasks or remaining in an awkward position for a long period of time. Such tasks can cause many employees to suffer job-induced injuries that may inhibit their ability to perform simple activities.
(1 hour) This course is designed for any employee who may be working at heights or any staff that may ever be around someone working at heights. The subject matter of the training includes ladders, handrails, stairs and basic fall protection equipment.
Employees required to use portable fire extinguishers (PFE) must receive training on the proper use, classification, maintenance, testing and storage of PFE. This training class will familiarize employees with the general principles of fire extinguisher use and the hazards involved.
(4 hours) Facilities using hazardous materials must develop and implement a Hazard Communication (HAZCOM) program that includes a written plan, employee training, chemical inventory and SDSs. Our training course will satisfy your employee training requirements and will educate your employees regarding their "right to know" about hazards in the workplace and the Globally Harmonized System for classification and labeling of chemicals.
Any employee who is required to respond and manage hazardous substance releases in a defensive manner through isolation, evacuation and containment from a safe distance needs this training. First responders at the operations level must have awareness-level training and at least 16 hours of additional operations-level-specific training, so this course is perfect. Upon successful completion, participants will receive a certificate of completion, which is accepted by OSHA as documentation of training.
(40 hours) This course provides certification for the 40-hour HAZWOPER Site Worker training, including necessary classroom instruction to meet the requirements of regulatory requirements for a HazMat employee. The course will cover hazardous waste safety, site hazards, chemical identification, decontamination and other key areas for your employees, including practicums to engage and educate your employees. This course takes a full five days and each participant must go through a one-day refresher every year.
(8 hours) This course provides the 8-hour hazardous materials first responder training at the awareness level, including necessary classroom instruction to meet the regulatory requirements. Instruction includes recognition of hazardous chemicals associated with spills and leaks within the workplace. The individual will learn notification, isolation and evacuation measures to protect employees under a site-specific emergency response plan.
(8 hours) This course provides annual recertification for all HAZWOPER first responder and site worker training, including necessary classroom instruction to meet the regulatory requirements for hazardous material response refresher training.
(2 hours) Any employee working in an area where they may be exposed to noise at or above 85-dB over an eight-hour period needs this training and the site needs a written hearing conservation program in place. This course trains employees on the hearing conservation program, causes of high noise levels, signs and symptoms of hearing loss, prevention of hearing damage and proper use, and maintenance of hearing protection.
(24 hours) This course meets the requirements that all miners and contractors exposed to the hazards of the mine be trained in mine-specific safety. MSHA requires a maximum of thirty (30) students per MSHA safety training course.
(10 hours) The OSHA 10-hour Outreach Training Program for construction is intended to provide entry-level construction workers information about their rights and employer responsibilities, as well as how to identify, abate, avoid and prevent job-related hazards on a construction site. The training covers a variety of construction safety and health hazards that workers may encounter at a construction site. All subjects are taught in accordance with current OSHA Training Institute guidelines and regulations by an OSHA-authorized instructor. OSHA requires that each course take place over a two-day period as no in-class time period is allowed to exceed seven-and-a-half hours per day.
(10 hours) The OSHA 10-hour Outreach Training Program for general industry provides training for workers and employers on the recognition, avoidance, abatement and prevention of safety and health hazards in the workplace. All subjects are taught in accordance with current OSHA Training Institute guidelines and regulations by an OSHA-authorized general industry outreach instructor. OSHA requires that each course take place over a two-day period and classroom time is capped at seven-and-a-half hours per day.
(30 hours) The OSHA 30-hour Outreach Training Program for construction is detailed training for supervisors and those construction employees with some safety responsibility. Training includes an overview about construction workers' rights, employer responsibilities and how to identify, abate, avoid and prevent job-related hazards on a construction site. All subjects are taught in accordance with current OSHA Training Institute guidelines and regulations by an OSHA-authorized instructor. OSHA requires that each course take place over at least a four-day period.
(30 hours) The OSHA 30-hour Outreach Training Program for general industry is detailed training for supervisors and those employees with some safety responsibility. All subjects are taught in accordance with current OSHA Training Institute guidelines and regulations by an OSHA-authorized general industry outreach instructor. OSHA requires that each course take place over at least a four-day period.
(4+ hours) This training is provided to employees who use, maintain or inspect energized equipment. The purpose of machine-specific lockout/tagout procedures is to guide an authorized employee through a sequential process that renders a piece of equipment or process safe. The course covers the site-specific LO/TO program and provides an overview of the signage, locks and policies needed to ensure the safe use and maintenance of mechanical equipment.
(2 hours) This training course provides managers, supervisors and employees critical information on how to follow the rules for proper PPE selection and use. Our training addresses the hazards and risks for employees in their workplace, the proper selection, inspection, maintenance and use of PPE such as eye, face, hand, foot, head and
body protection to ensure employees are protected during work tasks and effective evaluation for managers and supervisors of the employer PPE program.
(4+ hours) Operators of powered industrial trucks (PITs) must be trained and evaluated (at least every three years) before being assigned and allowed to operate a powered industrial truck (forklifts, aerial lifts, scissor lifts, hoists, etc.). This class will cover initial training for employees as well as any refresher training needed for the employer to recertify its employees.
(Annual requirement, time will vary)OSHA standards require employers to provide employees with respirators that are "applicable and suitable" for the purpose intended when such equipment is necessary to protect employees. Since a respirator can't protect if it doesn't fit properly, OSHA requires employers to fit-test workers who must wear tight-fitting respirators on the job. Arbill offers both qualitative (pass/fail) and quantitative (measurement of actual leakage).
(Class time will depend on respiratory equipment needed)OSHA mandates that employers develop and implement a written respiratory protection program for employees required to wear respiratory protection. This training will cover the site-specific program and will educate your employees about respiratory hazards in the workplace.
(4 hours) Owners or operators of regulated facilities must properly instruct their oil handling personnel in the operation and maintenance of equipment to prevent the discharge of oil. This training will ensure operating personnel have an adequate understanding of the SPCC plan for their facility and will highlight any known discharges, failures or malfunctioning equipment that occurred within the last year at the facility, including recently developed precautionary measures.
(4 hours) This course is instructor-led classroom training educating your employees on safe work procedures for "hot work." Your employees will be taught safe welding practices, proper identification and use of PPE, and how to identify the hazards of using compressed gasses or welding in a confined space. Training includes approximately four (4) hours of classroom training for up to fifteen (15) employees, and includes all training materials, a written examination and certificates of completion.
CONTACT US